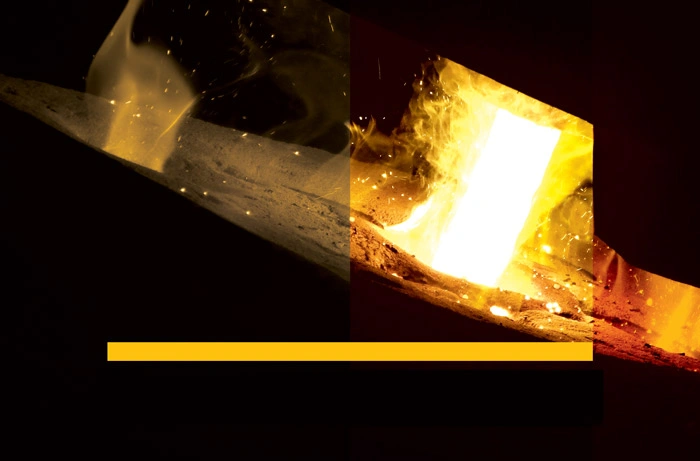
Ravanshir Steel Company
Ravanshir Steel Company was founded in 1985 and put into operation four years later in 1989. With over 30 years of experience, Ravanshir Steel Company is a leading supplier of equipment for pelletizing factories, as well as the cement, steel, and mineral processing industries (including iron, copper, aluminum, lead, and zinc). The company is ISO 9001:2015 certified and holds the “Quality Management System (QMS)” certificate. Leveraging advanced technical expertise, Ravanshir’s engineering team designs new equipment or reverse engineers existing equipment to ensure precision in the production process. As a pioneer in producing various industrial parts for Iran’s key industries, the company employs high-capacity induction melting furnaces (up to 10 tons), laboratory equipment, machining devices, and comprehensive after-sales services. With a team of experienced professionals, Ravanshir Steel prioritizes the continuous improvement of production speed, accuracy, and quality.
CEO's Message
Ali Hossein Salehi
Ravanshir Steel Company's CEO
Ravanshir Steel Company operates in the fields of casting and production of steel, cast iron, alloy, and non-alloy components. The product range of this company includes various parts used in the cement industry, mining, mineral processing, and metal industries (steel, aluminum, copper, etc.).
Our goal at Ravanshir Steel Company is to utilize up-to-date knowledge, creativity, innovation, and modern technologies in order to develop and expand the current potential borders through close interaction with our customers.
Our vision is for Ravanshir Steel to achieve national recognition so that customers use our products with satisfaction, trust, and confidence and remain loyal to the company’s name and brand.
In this regard, we ask all our respected colleagues at all organizational levels to work with precision, capability, a positive attitude, and extra effort to elevate the name of Ravanshir Steel and to take steps toward achieving the following goals. We hope for continuous success and presence at the pinnacle of Iran’s industry.
- Maintain and enhance Ravanshir Steel’s position as one of the leading brands in the casting industry.
- Develop production lines and increase the design capacity of casting equipment.
- Enter global markets in the casting field, with continuous progress and development.
- Train managers, engineers, and experts specialized in the casting industry.
Ravanshir Steel; Getting to know the strong pillars of Iran's foundry industry
Ravanshir Steel Company is composed of various and coordinated units, each with its own specific responsibilities, striving to provide casting services of the highest quality to its customers.
Sales engineering, contracts, and after-sales services are subsets of this unit, a customer-related department whose top priority is providing the best possible customer service. This department’s mission is to respond quickly and be at the customer’s site throughout all working stages.
The Design and Engineering department creates documents and technical drawings after the commercial department completes customer contracts. Technical drawings of the patterns are created using AutoCAD and CATIA software. After that, the casting simulation software (Procast and SUTcast) is used to finalize drawings and send them to the production department. It is important to note that Ravanshir Steel Company’s pattern-making workshop uses the most cutting-edge manufacturing equipment, such as three-axis CNC machines, 3D printers, and others, to create all kinds of patterns based on drawings from the Design and Engineering unit.
The production unit of Ravanshir Steel Company is divided into several subcategories with the goal of producing casting tools and equipment. Sections such as molding, alloying, melting, grinding, cleaning, and heat treatment work together to produce the parts you need with the highest quality.
Ravanshir Steel Company, leveraging its skilled and experienced experts in the field of casting, ensures precise and continuous monitoring of raw materials and products throughout the entire production process using advanced laboratory equipment.
Raw Material Quality Control
In the raw material section, various aspects such as the evaluation of different sands, binders, ferroalloys, scrap metals, and other inputs are carefully monitored.
Quality Control During Production Stages
Quality control throughout the various production stages is conducted based on standardized procedures outlined in the product quality plan developed by the company’s technical committee. These checks are performed step by step in processes such as molding, assembly, melting, unloading, grinding, and heat treatment.
Quality Control During Molding
In the molding stage, samples are randomly taken from the mixture of sand and binder and are tested for compressive and shear strength while in a wet state.
Quality Control in the Melting Process
The most critical stage in the quality control unit is the melting process, where aspects such as chemical composition analysis, pouring temperature, pouring duration, and tracking number registration are closely monitored. With the use of a spectrometer, which serves as the core of the casting unit, trained personnel oversee the alloying and monitoring of various melts.
Quality Control in Heat Treatment
In the heat treatment section, supervision ensures that the thermal cycles are executed correctly according to the product quality plan. Moreover, thermocouples used in furnaces are inspected as per internal guidelines, and any deviation in temperature results in the immediate removal of the thermocouple from service.
Final Product Control
At the end of the production process, the final product undergoes a thorough inspection. Key procedures in this phase include dimensional checks based on technical drawings, non-destructive testing (PT and UT), and hardness testing of the parts. Only when these tests are passed does the product receive approval to enter the warehouse as a quality-certified item.
This department, with the help of sales and technical engineering employees, has carried out its research projects according to up-to-date science to continuously improve our products and meet our customers’ needs and goals. As a result, product efficiency has increased by up to 30%, particularly in the milling and slurry pump parts.
Ravanshir Steel Company’s operations are fully aligned with the ISO 9001:2015 Quality Management System, overseen by SGS, ensuring all units comply with rigorous control protocols.
Our Clients
At Ravanshir Steel, we are proud to have collaborated with a wide range of industries in the casting sector across the country. Our successful projects in the production of casting tools, industrial parts, and equipment have made us one of the main choices for reputable companies in the steel, cement, and mining industries.
Steel and pellet industries
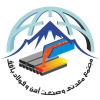
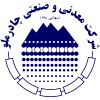
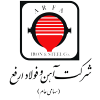
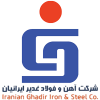
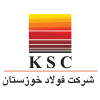

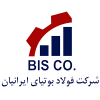
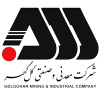
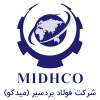
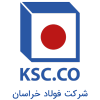
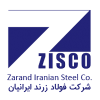

Cement industries
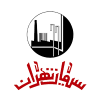
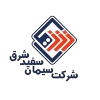
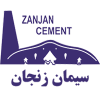
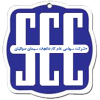
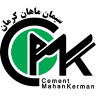
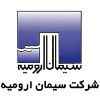
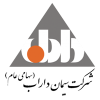
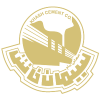
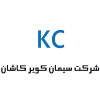
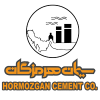
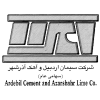
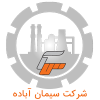
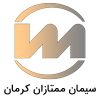
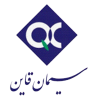
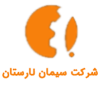
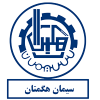
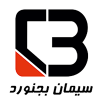
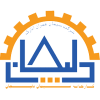

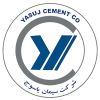
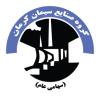
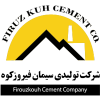
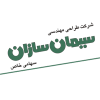
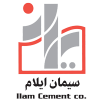
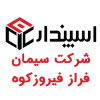

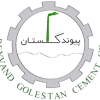
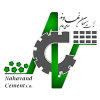
Mining industries
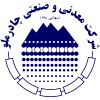
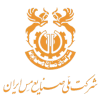
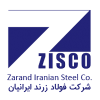
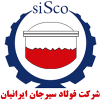
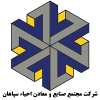
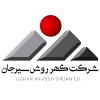
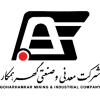
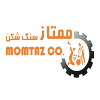
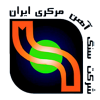
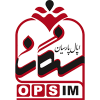
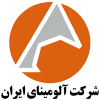
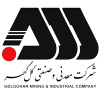
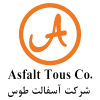
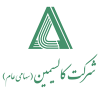
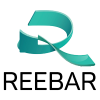
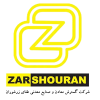
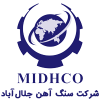
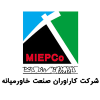